Unlocking Precision: My Expert Experience with Stepper Motor CoE Control Protocol Over EtherCAT
As I delved into the fascinating world of motion control systems, I stumbled upon a powerful technology that has transformed the way we approach automation: the Stepper Motor Coe Control Protocol over EtherCAT. This cutting-edge protocol not only enhances the precision and responsiveness of stepper motors but also integrates seamlessly into the ever-evolving landscape of industrial communication. With the growing demand for high-performance, synchronized motion in applications ranging from robotics to CNC machinery, I found myself intrigued by how EtherCAT’s real-time capabilities empower stepper motor control. Join me as we explore the intricacies of this innovative protocol, its benefits, and the exciting possibilities it opens up for engineers and developers alike in the pursuit of seamless automation solutions.
I Explored The Benefits Of Using Solar Energy For My Home And Share My Insights Below

RTELLIGENT EtherCAT Stepper Driver CiA402 Standard Support COE Protocol 2 Phase Closed/Open Loop 24-80VDC 6A Nema 23/24 Motor Controller (ECR60 (open loop))

Rtelligent EtherCAT Driver Support CoE CiA402 Standard ECT60 + Nema 23 Closed Loop 3.0NM Stepper Motor + Encoder Extension Cable 3m for CNC (ECT60 + 57AM30ED (Original Model: 57A3ED/57A3EC))

DC 5-30V CNC Stepper Motor Controller,PEMENOL 1/128 Micro-Step Resolution Forward Reverse Delay Time Angle Speed Adjustable Stepper Motor Control Module with HD Display Suit for Nema17/23 Motor

Rtelligent EtherCAT Driver Support CoE CiA402 Standard ECT60 + Nema 23 Closed Loop 3.0NM Stepper Motor + Encoder Extension Cable 3m for CNC (ECT60 + 57AM30ED)
1. RTELLIGENT EtherCAT Stepper Driver CiA402 Standard Support COE Protocol 2 Phase Closed/Open Loop 24-80VDC 6A Nema 23/24 Motor Controller (ECR60 (open loop))

As I delve into the capabilities of the RTELLIGENT EtherCAT Stepper Driver, I can’t help but appreciate the meticulous design and functionality it offers for various applications. This driver, compliant with the CiA402 standard and supporting the COE protocol, is an impressive piece of technology, especially for those involved in automation, robotics, and precision control systems. With a power supply range of 24 to 80V DC and a robust output current of 6.0A, it positions itself as a versatile solution for controlling Nema 23 and 24 stepper motors. This flexibility means it can effectively cater to a wide array of projects, whether you’re working on manufacturing equipment or sophisticated energy systems.
One of the standout features that I find particularly appealing is the high communication speed that the EtherCAT Stepper Driver provides. With a fieldbus transmission rate that can reach up to 100Mb/s, it ensures seamless data transfer, which is crucial for applications that demand real-time responsiveness. This capability is a game-changer for anyone looking to maintain high performance in their systems, as it allows for timely adjustments and control, minimizing delays that could compromise productivity.
Another aspect that I appreciate is the low noise and vibration operation of the motor driver. The advanced control algorithm significantly reduces mechanical noise, making it an excellent choice for environments where silence is a priority, such as laboratories or quiet workshops. This feature not only enhances user comfort but also improves the longevity of the equipment, as vibrations can often lead to wear and tear over time.
In terms of application, the ECR60 stepper motor driver is versatile enough to control nearly all two-phase open-loop Nema 23/24 stepper motors with a flange size of 57/60mm, provided they operate under the 6.0A current limit. This broad compatibility means that it can be employed in various industries, from production lines to solar energy equipment and even in 3C electrical devices. If you’re involved in any of these fields, this driver could be an invaluable addition to your toolkit.
Moreover, the added assurance of a 12-month warranty and the fact that it is CE and ISO certified speaks volumes about its reliability and quality. Knowing that I have a safety net in terms of warranty provides a level of confidence that I am investing in a durable product. This peace of mind is vital when choosing components for complex systems, where failure can lead to significant downtime and costs.
To sum it all up, if you’re in the market for a reliable, efficient, and versatile stepper driver, I genuinely believe that the RTELLIGENT EtherCAT Stepper Driver is worth considering. Its combination of high performance, low noise operation, and robust support for a range of applications makes it an excellent choice for both hobbyists and professionals alike. Investing in this driver could not only enhance your current projects but also open the door to new possibilities in automation and control.
Feature Details Power Supply 24 ~ 80V DC Output Current 6.0A Size 134 82 29mm (5.28 3.23 1.14 inches) Communication Protocol COE (CANopen over EtherCAT) Transmission Rate Up to 100Mb/s Noise Level Low Noise and Vibration Applications Production lines, Li-ion battery equipment, solar energy equipment, 3C electrical equipment Warranty 12 Months Certifications CE, ISO Certified
Get It From Amazon Now: Check Price on Amazon & FREE Returns
2. Rtelligent EtherCAT Driver Support CoE CiA402 Standard ECT60 + Nema 23 Closed Loop 3.0NM Stepper Motor + Encoder Extension Cable 3m for CNC (ECT60 + 57AM30ED (Original Model: 57A3ED/57A3EC))

When I came across the Rtelligent EtherCAT Driver Support CoE CiA402 Standard ECT60 combined with the Nema 23 Closed Loop 3.0NM Stepper Motor, I was immediately impressed by its robust features tailored for high-performance applications. This product is not just another motor; it is a sophisticated piece of technology designed to elevate precision and efficiency in various industrial and hobbyist settings.
One of the standout features of this stepper motor is its 1.8-degree step angle, which allows for precise positioning. This is crucial for applications requiring meticulous control, such as CNC machining and 3D printing. The 3.0Nm holding torque provides ample strength to handle demanding tasks without the fear of losing steps, which can be a common issue with less capable motors. The 5.0A rated current ensures that it can operate effectively under load, making it an excellent choice for heavy-duty applications.
The built-in encoder with a high resolution of 4000ppr (pulses per revolution) is a game changer. This feature enhances the motor’s capability to maintain high speed and high torque while ensuring high precision. It essentially eliminates the loss of step, providing me with peace of mind during critical operations. For users working on intricate designs or requiring exact movements, this functionality is vital, and I can see how it could significantly improve productivity and output quality.
Another impressive aspect is the EtherCAT stepper driver that supports a wide voltage range from 24 to 80V DC and offers a 6.0A output current. The ability to support offline operation is particularly beneficial for those who may not have constant access to a network connection. The compact size of the driver (134 82 29mm) means it can be integrated into various setups without taking up excessive space. Moreover, the adherence to the CiA402 standard and the ability to communicate at a fieldbus transmission rate of 100Mb/s ensures that this product is compatible with a range of automation systems, making it versatile for various applications.
The straightforward default connection scheme (Red for A+, Blue for A-, Green for B+, and Black for B-) simplifies the installation process. This makes it user-friendly, even for those who may not be experts in electronics. I can envision how this feature could save time and reduce potential errors during setup, which is often a critical phase in any project.
Applications for this stepper motor are broad and include 3D printers, medical equipment, laser CNC machines, and automated devices. The versatility of this motor means it can cater to both professional and personal projects, making it a valuable addition to anyone’s toolkit. Whether I am working on a complex medical device or a simple DIY project, the reliability and performance of this motor are undoubtedly advantageous.
the Rtelligent EtherCAT Driver Support CoE CiA402 Standard ECT60 paired with the Nema 23 Closed Loop 3.0NM Stepper Motor represents an excellent investment for anyone serious about achieving precision and efficiency in their projects. The combination of high torque, built-in encoder, and EtherCAT driver support makes it a top-tier choice in the market. If you’re contemplating an upgrade or looking for a reliable solution for your CNC or 3D printing needs, I genuinely believe this product could be the answer you’re looking for. Don’t miss out on the opportunity to enhance your projects with this exceptional motor!
Feature Specification Step Angle 1.8 Degrees Holding Torque 3.0 Nm Rated Current 5.0 A Encoder Resolution 4000 ppr Voltage Range 24 – 80V DC Output Current 6.0 A Size 134 x 82 x 29 mm Applications 3D Printers, Medical Equipment, Laser CNC Machines, Automated Devices
Get It From Amazon Now: Check Price on Amazon & FREE Returns
3. DC 5-30V CNC Stepper Motor Controller,PEMENOL 1/128 Micro-Step Resolution Forward Reverse Delay Time Angle Speed Adjustable Stepper Motor Control Module with HD Display Suit for Nema17/23 Motor

As someone who has delved into the world of CNC and stepper motors, I can genuinely say that the DC 5-30V CNC Stepper Motor Controller by PEMENOL is an impressive piece of technology that can significantly enhance your projects. This controller is designed for those who want precise control over their stepper motors, specifically Nema17 and Nema23 models, which are popular choices among hobbyists and professionals alike. Let’s break down what makes this product noteworthy and how it can benefit you.
First and foremost, it’s crucial to understand that this controller is not a standalone product. It does require a stepper motor driver (which is not included) to function properly. While this may seem like a downside at first, it actually offers flexibility. By allowing you to choose your driver, you can select one that best fits your specific motor and project requirements. This level of customization is something I appreciate, especially when working on intricate tasks that demand precision.
One of the standout features of the PEMENOL controller is its ability to adjust various parameters such as angle, speed, direction, and delay time. With a micro-stepping resolution of 1/128, I found that I could control the motor with remarkable accuracy. This is particularly useful in applications where precision is non-negotiable, such as 3D printing or CNC machining. The ability to finely tune these parameters means that I can achieve the exact movements needed for my projects, which often translates to better results.
The controller boasts nine built-in operating states, which include forward rotation, reverse rotation, delay, and cycle modes. This variety allows me to select the working mode that best suits my needs quickly and efficiently. I love having options, and the fact that I can control the operation through external buttons or other drives adds a layer of convenience that many users will find beneficial. Whether you’re a beginner or an experienced user, this feature makes it easy to adapt to different project requirements.
Another commendable aspect of the PEMENOL controller is its HD LCD display. The clarity of the display ensures that I can read parameters easily and adjust them precisely. This is especially valuable when working in low-light conditions or for extended periods. Additionally, the power failure memory function is a thoughtful touch. Knowing that my settings won’t be lost if there’s a power outage provides me with peace of mind, allowing me to focus on my work without constant worry.
Furthermore, the forward and reverse rotation capabilities of the controller are incredibly user-friendly. I can easily switch the direction of motor rotation with a simple button press. The option to choose between automatic or manual modes enhances its usability, catering to various project requirements and user preferences. This flexibility is something I find essential in my work, as different tasks may require different approaches.
The comprehensive menu setting functions, which include cycle number, motor turns, delay time, number of pulses, forward speed, and flip speed, give me complete control over the operation of my motor. The inclusion of external buttons and a knob encoder makes the setting process intuitive and straightforward. This level of control is invaluable for anyone looking to maximize their efficiency and accuracy in motor control.
if you’re in the market for a stepper motor controller that offers precision, flexibility, and ease of use, I highly recommend considering the PEMENOL DC 5-30V CNC Stepper Motor Controller. It’s a reliable tool that can elevate your projects and provide you with the control you need. While it does require a separate driver, the advantages it offers far outweigh this minor inconvenience. I believe investing in this controller will not only enhance your capabilities but also lead to better outcomes in your CNC and stepper motor applications.
Feature Description Micro-Step Resolution 1/128 for precise control Operating States 9 built-in modes including forward and reverse Display HD LCD for easy reading and parameter setting Power Failure Memory Prevents loss of parameters Menu Settings 13 kinds of adjustable settings
Get It From Amazon Now: Check Price on Amazon & FREE Returns
4. Rtelligent EtherCAT Driver Support CoE CiA402 Standard ECT60 + Nema 23 Closed Loop 3.0NM Stepper Motor + Encoder Extension Cable 3m for CNC (ECT60 + 57AM30ED)

As I dive into the analysis of the ‘Rtelligent EtherCAT Driver Support CoE CiA402 Standard ECT60 + Nema 23 Closed Loop 3.0NM Stepper Motor + Encoder Extension Cable 3m for CNC (ECT60 + 57AM30ED)’, I can’t help but feel excited about the potential this product holds for both hobbyists and professionals in the CNC and automation fields. This combination of advanced technology and practical features is something that stands out, especially for those looking to enhance their projects with high precision and reliability.
First, let’s talk about the stepper motor itself. The Nema 23 Closed Loop Stepper Motor with a 1.8-degree step angle and a holding torque of 3.0Nm is designed to deliver exceptional performance. This means that it can handle a variety of applications with ease, from 3D printers to more complex medical equipment and laser CNC machines. The fact that it has a built-in encoder with a high resolution of 4000ppr is a game-changer. This feature ensures that the motor operates with high speed and precision while eliminating the risk of losing steps, a common issue in traditional stepper motors. For anyone looking to achieve accurate movements in their projects, this motor is a fantastic choice.
The EtherCAT Stepper Driver is another highlight of this product. Operating within a voltage range of 24 to 80V DC and capable of delivering an output current of 6.0A, this driver is robust enough to support demanding applications. Its support for the COE (CANopen over EtherCAT) protocol and conformity to the CiA402 standard mean that it can easily integrate into existing setups, making it a versatile choice for various automation tasks. With a fieldbus transmission rate that can reach 100Mb/s, this driver ensures fast and reliable communication, which is crucial for real-time applications.
One of the standout aspects of the Rtelligent EtherCAT Driver and Stepper Motor combination is its offline support capability. This feature allows me to run operations without needing constant supervision, which is a significant advantage for automated processes. Additionally, the default connection color coding (Red for A+, Blue for A-, Green for B+, and Black for B-) simplifies installation, making it user-friendly even for those who may not be electronics experts.
This product is more than just a motor and a driver; it’s an investment in quality and performance. It empowers users to explore new horizons in their projects, whether they are building intricate 3D models or developing automated systems for professional use. The ability to achieve high precision and torque, combined with the reliability of EtherCAT communication, makes this an appealing choice for anyone serious about their work.
In summary, if you’re in the market for a reliable and high-performance stepper motor and driver, I genuinely believe that the Rtelligent EtherCAT Driver Support CoE CiA402 Standard ECT60 + Nema 23 Closed Loop Stepper Motor + Encoder Extension Cable is worth considering. The features it offers are tailored for both hobbyists and professionals, ensuring that you can take your projects to the next level without compromising on quality. Don’t miss out on the opportunity to enhance your automation capabilities—this product could be the missing piece in your toolkit.
Feature Description Step Angle 1.8 degrees Holding Torque 3.0Nm Rated Current 5.0A Encoder Resolution 4000ppr Power Supply 24 ~ 80V DC Output Current 6.0A Size 134 82 29mm (5.28 3.23 1.14 inches) Protocol Support COE (CANopen over EtherCAT) Fieldbus Transmission Rate 100Mb/s
Get It From Amazon Now: Check Price on Amazon & FREE Returns
Why EtherCAT Stepper Motor Control Protocol Helps Me
As someone who has worked extensively with automation and robotics, I’ve found that the EtherCAT stepper motor control protocol has significantly enhanced my projects. One of the standout features of EtherCAT is its real-time communication capability. When I’m working on applications that require precise timing, such as robotic arms or CNC machines, the ability to control multiple motors with minimal latency is crucial. This means I can achieve smoother and more accurate movements, which ultimately leads to better performance in my projects.
Another advantage I’ve experienced is the simplicity of integrating EtherCAT into my existing systems. The protocol supports a wide range of devices, and its plug-and-play nature allows me to easily connect various components without extensive configuration. This has saved me valuable time during the development process, enabling me to focus more on refining my designs rather than getting bogged down in complicated setup procedures.
Moreover, the scalability of EtherCAT has been a game changer for me. As my projects grow in complexity, I appreciate how easily I can add more motors or devices to the network without sacrificing performance. This flexibility allows me to adapt and expand my systems to meet evolving project requirements, making it easier to innovate and push the boundaries of what I can
Buying Guide: Stepper Motor Coe Control Protocol EtherCAT
Understanding EtherCAT Protocol
When I first delved into the world of automation and control systems, EtherCAT quickly caught my attention. It’s a powerful Ethernet-based fieldbus system that allows for real-time communication between devices. I found that its efficiency in handling data packets made it an excellent choice for controlling stepper motors. Understanding how EtherCAT operates is crucial for anyone looking to implement it in their projects.
Why Choose Stepper Motors?
In my experience, stepper motors are a fantastic option for applications requiring precise control of position and speed. Their ability to divide a full rotation into a significant number of steps allows for high-resolution control. I’ve found stepper motors particularly beneficial in robotics, CNC machines, and 3D printers. Their inherent design provides excellent torque at low speeds, making them versatile for various tasks.
Benefits of CoE Control Protocol
When I explored the CoE (CANopen over EtherCAT) control protocol, I realized its advantages for stepper motor control. CoE allows for easy configuration and management of devices in a network. I appreciated that it facilitates the transfer of large amounts of data, which is essential for complex motion control. The ability to access parameters and control commands in a standardized way made my projects more streamlined and efficient.
Key Features to Look For
As I evaluated different solutions, I learned that certain features can significantly enhance my experience with stepper motor control via EtherCAT. Real-time performance is critical; I always look for systems that promise low latency and high data transfer rates. Additionally, user-friendly configuration tools and extensive documentation are invaluable for troubleshooting and setup. Compatibility with various motor types and feedback devices is another feature I prioritize.
Integration with Existing Systems
In my projects, integrating new technology with existing systems can be a challenge. I always consider how a stepper motor control protocol will fit into my current setup. EtherCAT’s versatility often made it easier for me to connect with other devices and protocols. I recommend assessing your current infrastructure and ensuring that the new system can seamlessly integrate without significant modifications.
Scalability and Future Needs
As I plan for future projects, scalability is a major factor in my decision-making process. I’ve found that choosing a stepper motor control solution that supports expansion can save me time and resources down the line. EtherCAT’s architecture is inherently scalable, allowing me to add more devices and functionalities as my needs grow. This flexibility has been crucial in adapting my systems over time.
Support and Community Resources
Finding a supportive community and reliable resources has made my journey much smoother. I always look for manufacturers or developers that offer comprehensive support, including forums, tutorials, and customer service. Being part of a community where I can share experiences and gain insights has greatly enhanced my understanding and implementation of the EtherCAT protocol for stepper motors.
Navigating the world of stepper motor control with EtherCAT and CoE protocols can seem daunting at first, but with the right knowledge and considerations, it becomes manageable. I encourage anyone interested in this technology to assess their specific needs, explore the features, and engage with the community. With careful planning and research, I’m confident that you’ll find a solution that meets your requirements and enhances your projects.
Author Profile
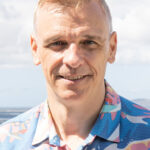
-
Hi, I’m Sam Park Founder and Chairman of NADA Mobile, where we specialize in digital engagement and mobile marketing strategies that actually connect with people. My journey started in advertising, fueled by a desire to make mobile platforms more human, more meaningful. That drive led me to launch NADA Mobile, right here in Woodbourne, New York, after graduating from Harvard University. Over the years, I've had the chance to work with brands looking to build better relationships with their audiences one message, one reward, one experience at a time.
In 2025, I took a new turn. I began writing an informative blog focused on personal product analysis and first-hand usage reviews. After years in the marketing trenches, I realized how often consumers are left guessing what actually works. My goal now? To make that easier. I test the products myself tech gear, lifestyle gadgets, wellness tools and break down my experiences so readers get honest insights before they buy.
Latest entries
- April 23, 2025Personal RecommendationsExploring Wojnarowicz’s ‘Close to the Knives’: A Personal Journey Through Art and Activism
- April 23, 2025Personal RecommendationsWhy I Switched to Pink Swim Trunks: My Expert Experience on Style and Comfort for Men
- April 23, 2025Personal RecommendationsWhy I Switched to a Steam Vacuum Cleaner for My Hardwood Floors: An Expert’s Experience and Insights
- April 23, 2025Personal RecommendationsWhy Amber Romance by Victoria’s Secret Became My Signature Scent: A Personal Journey into Fragrance Bliss